We provide various casting process and brings many unique benefits to our customers. We have built three casting plants in the past 15 years in order to offer you more casting solutions. We have committed to our customers cost efficiency, freedom of design, reproducibility, reduced machining and increased performance. As we started as an investment casting foundry, we know details of this metal-forming technique. Investment Steel Casting China casting is also known as lost wax casting. Basically, it refers to make a wax pattern formed with a ceramic. Then, melting the wax makes the ceramic empty. Eventually we get the casting after pouring the metal into the ceramic. We continue to improving our process and utilizing the newest technology available in our industry.
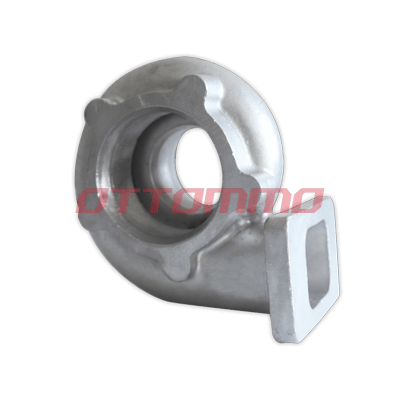
Water Glass and Silica Sol Investment Casting: Water glass and Silica sol casting make china casting industry special all over the world. The main differences are the surface roughness and the casting price. Most foundries made casting our of water glass process in China 10 years ago. Only few casting foundries change to silica sol process nowadays. However, we keep both processes and make more options for our customers.
Water Glass Investment Casting Method: We use domestic wax and dewax into high temperature water. Most importantly, ceramic mold material is water glass quartz sand that is very cheap locally. Therefore, the surface finish and the accuracy of the casting will not be that good. But it is still weight better than sand casting process.
Silica Sol Investment Casting Method: We use high temperature wax and dewax into flash fire. Meanwhile, ceramic mold material is silica sol zircon sand that is more expensive than quartz sand. Therefore, the surface finish and the accuracy of the casting will be very impressive. Silica sol investment casting is our main production line right now.
Vacuum Casting: Vacuum casting capability makes it special to you. We can make quality and complex castings by our vacuum furnace with low price. The only one difference between normal investment casting and vacuum casting is pouring process. In order to achieve optimal casting properties, we have to pour the metal into vacuum furnace. We melt high nickel alloy or supper alloy and pour the metal by evacuating air in an enclosed area. As a result, we can achieve complex and difficult castings successfully.
For more information click here ->>Precision Casting